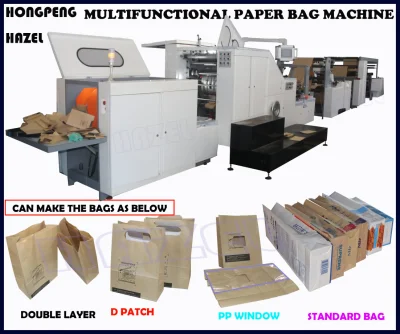
Paper Bag Making Machine Square Bottom with 2 Colors, 4 Colors on Line
Item 1 Adjustable Roll to Square Bottom Paper bag making machine Application:This machine is designed to manufacture squ
Basic Info
Model NO. | SBR |
Size and Shape | 7700X1700X2100 |
Long | 190-370 |
Weight | 4200 |
Material | Paper |
Usage | Shopping Bag, Garment Bag, Leisure Food Bag, Bread Bags, Airsickness Bag, Fruit Bag |
Speed Adjust | Inverter Control |
Material Loading | Hydraulic Loading |
EPC | Simulated EPC |
Tension | Auto Tension |
Glue | Auto Glue |
Computer | PLC Control |
Transport Package | by Iron Pallet |
Trademark | hongying |
Origin | China |
HS Code | 8441200000 |
Production Capacity | 10sets /Month |
Product Description
Item 1Adjustable Roll to Square Bottom Paper bag making machine
Application:This machine is designed to manufacture square bottom paper bags from paper roll in blank or printed. Side gluing, tube forming, cutting, bottom creasing, bottom gluing, bottom forming and final product out feed can be completed within one time by this machine. It is ideal equipment for making paper bag for foodstuff bag, shopping bag and so on. Controlled by PLC system, equipped with in-touch screen and servo motor for bag length control, this machine can produce different size paper bag
TECHNICAL PARAMETER
MODEL SBR-180
Width of Paper roll ............................................................. 600mm
Length of Bag ..................................................................... 190-370mm
Width of Bag ....................................................................... 80-180mm
Width of laterial M gusset .......................................................... 50-100mm
Paper weight .........................................................................50-120g/m2
Max. Diameter of Paper Roll ...............................................ф1400 mm ( 59" )
Internal Diameter of Roll Core..............................................ф76 mm ( 2.99" )
Max.Speed ............................................................................200 pcs/min
Total Power ...........................................................................10Kw
Weight of Machine ...............................................................Approx 6500 kg
Overall Dimension................................. 9200x1600x1700mm
Bottom
Tube Length
Item 2
Performance and Features:
- Adjustable roll to square bottom bag making machine
- Introduce In-touch screen human-machine interface, easy for correction and fine adjustment. Alarm and working status can be displayed in screen on-line, easy for operation and maintenance.
- Equipped with Mitsubishi PLC for centralized control system and SICK photocell for correction, tracking the printed material accurately, minimize the adjustment and preset time, increase the production efficiency.
- Human oriented security protection, whole housing design, ensure the safety of operator.
- physiosis roller hydraulic material loading system with chuck, hydraulic up/down system
- Automatic constant tension control for unwinding, EPC web guider system, motor for material feeding with inverter, minimize the adjustment time for web alignment.
- High speed oriented design ensure successful of production: within the suitable paper range, production capacity can reach 150~200pics/min, even higher. Increased the unit production capacity and higher profit.
- Original SCHNEIDER electric system, ensure better stability and reliability; perfect after sale service, trouble free for customer.
* Bag Dimension, Adhesive Quality, Operator Knowledge, % Moisture, Type and Basis weight of Paper Can affect Machine Speeds.
Main Configuration
1.Unwind Section
Structure, Features:
(1) Separated single unwind rollstand with hydraulic lift device.
(2) physiosis roller for paper roll loading, the load arms are driven by two hydraulic cylinders separately, can be adjusted arbitrarily.
(3) magnetic powder brake and constant auto tension control for unwinding tension control.
(4) EPC (electronic program control )web guide system for material alignment.
Parameter, Specification:
(1) Unwind Rollstand.................................................One (1) Supplied
(2) hydraulic lift device for material load .....................1 Set
Hydraulic Cylinder 100X500 .........................................................1 PC
Motor for hydraulic pump(1.5kw)............................................1 Unit
(3) Roll load Arm Switching Device .....................................................1 Set
(4) physiosis roller chuck Device ....................................................1 Set
(5) Magnetic Powder Brake (100N.m) ................................................. 1 Unit
(6) Tension transducer ....................................................................... 1PC
(7) EPC web guider system for material edge alignment ........................1 set
Sensor, Motor for drive, Hydraulic Cylinder, Hydraulic Pump etc.
2.Material In-feed Section
Structure, Features:
(1) Separated Material In-feed section
(2) Adjustable side seam glue coating, automatic disengage when machine stop
Parameter, Specification:
(1) Adjustable Side Seam Glue Coating (Seam Paste Stand-One (1) Ply Bag) :1 Set
Parts for Lateral Adjustment of Seam Glue Applicator
Photo-eye for Controlling Preprint Registration
3.Tube Forming Section
Structure, Features:
(1) Whole unit tube forming frame
(2) Former Mould Support Design,Adjustable Former Support for Precise Former Alignment
(3) Multi Side Tuck Discs Design, Manual Adjustment.Rotary Side Gusseting Tuck Disc-Quick Release Paper Threading & Save Production Setting
(4) Adjustable Pressing Wheel
Parameter, Specification::
(1) Adjustable Former Support Device .................................... 1 Set
(2) Side Tuck Device ........................................................... 1Set
Side Tuck Discs .............................................................Each 6 for left and right
Manual Adjustment Device ................................................ 2Set
(3) Pressing Wheel ................................................................... 5 Set
4.Bottom Forming Section
Structure, Features:
(1) Material feeding by INDEPENDENT SERVO Draw roll Drive System, Photo Cell System for Running Preprinted Materials (No Change gears)
(2) Rotary Serrated Cutoff with Elliptical Gears
(3)Adjustable Bottom Score Device, can adjust the bag bottom size,
(4)Bottom Opening Cylinder with Split Cam for Full Range Stretch Adjustment
(5) Multi Layer Bottom Forming Drum, Center Grippers, Second Tuck Clamps, and Drum Fingers are adjustable for ease of changeover.
(6) Bottom Glue Applicator with Pneumatic Cylinder for engagement
(7)Bottom Impressing Roller with up/down Feature for Easy Operation
Parameter, Specification:
(1) Tube Length Repeat Tolerance: Nominal tube Length +/- 0.5 mm
(2) Servo Motor: (Yaskawa).................................................. 2 Unit
(3) Serrated Cutoff Knife ................................................................1 Set
(4) Bottom Score Device.................................................................1 Set
(5) Bottom Opening Device ............................................................1 Set
6) Bottom Form Drum ...................................................................1 Set
(7) Bottom Glue Applicator............................................................ 1 Set
(8) Bottom Folder .......................................................................... 1 Set
5.Bag Delivery Section (standard from the Seller)
Structure, Features:
(1) Side Table Delivery with Belt for easy operation
(2) Rubber impress roller for Bag Shape Fixation
Parameter, Specification:
(1)Delivery Table.................................................................................1Set
(2)Conveying Belt .............................................................................. 2PC
6.Control Section
Structure, Features:
(1) PLC centralized control for whole machine.
(2)Human-machine Interface: Touch Screen Operator Control. Ease of Machine Setup for Repeat Changes & Monitoring
Parameter,Specification::
(1)PLC (Yaskawa)...................................................1Unit
(2)In-touch Screen 10″ (Yaskawa).........................1Unit
7.Others
(1) Main Components introduce NSK ball bearing from Japan
(2) Pneumatic Components: Airtag
(3)Low Voltage Components: SCHNEIDER.
(4) Side glue system using Italian ZATOR. Correction using Italian SELECTRA(ST)
(5) SICK photocell for correction, tracking the printed material accurately
(6) Servo Motor Yaskawa ,and Electric equipments SCHNEIDER.
Send to us